DISPOSAL
The company has been disposing waste since the mists of time; 1976 to be more precise. It is based on two main activities: physical/chemical waste processing and stabilisation. These two processes use hydraulic binders.
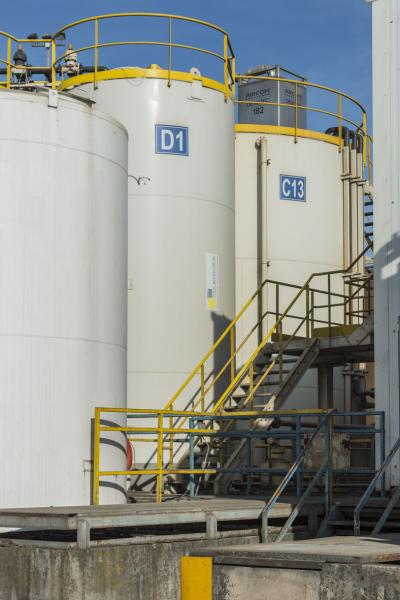
PHYSICAL/CHEMICAL PROCESSING
Physical/chemical processing is one of the two flagship activities implemented by REVATECH, processing at least 60,000 tonnes/year of mainly liquid, but also sludge and solid waste.
REVATECH has significant storage capacities. REVATECH defines the day-to-day make-up of its processing and production projects depending on its various stocks and on the basis of the composition of the waste it stores.
Waste is injected into high-capacity reactors, and water and reagents are added to produce homogeneous mixtures rendering the precipitated metals harmless.
REVATECH has an ongoing cyclic waste-to-waste principle, promoting the use of waste to treat other waste.
The mixtures obtained in this way are then filtered and the filtrates separated from the sludge using filter presses.
The filtrates are then treated in a physical/chemical purification facility, while the filter cakes are disposed of in engineered landfill sites as stabilised waste.
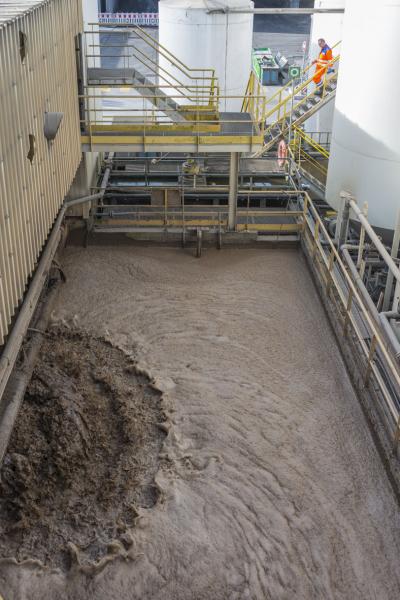
BIOLOGICAL PROCESSING
REVATECH runs a biological processing plant (activated sludge) operating with pure oxygen.
This processing plant takes biodegradable liquid waste of a biodegradability level higher than 70% and whose COD can be very high and may reach up to 200,000 mg/l.
The treated aqueous effluents mainly come from the chemical industry sector and metal surface processing.
These effluents, stripped of their metals and with adjusted pH, are then treated in a biological purification station whose capacity is 1000 kg of COD/day, the activated sludge of which consumes pure oxygen.
This activated sludge is regularly purged and filtered via filter presses. The cakes thus produced are then treated in order to stabilise them, and are then sent to engineered landfill sites.
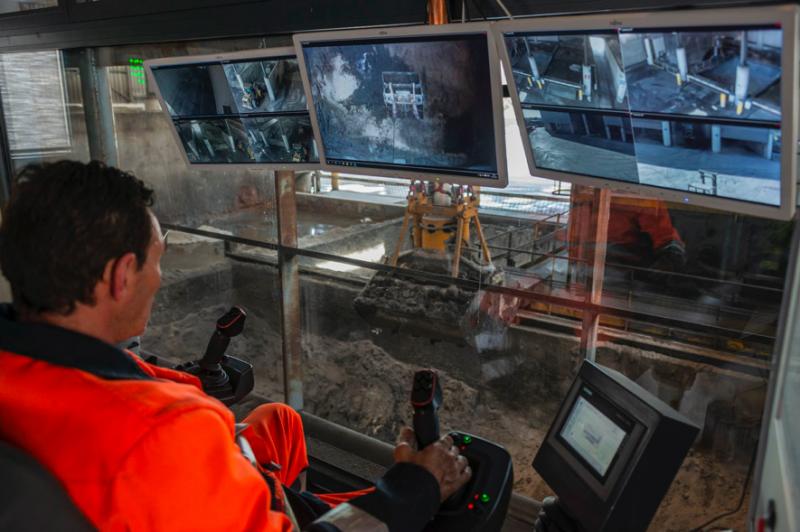
STABILIZATION
REVATECH was one of the first processing centres to implement stabilization processing.
Stabilization makes it possible to embed heavy metals in mineral matrices and insolubilize them.
The stabilization technique uses hydraulic reagents and pozzolanic binders.
REVATECH processing has evolved considerably over time.
Initially, the PETRIFIX process was used.
Abandoned with time, this process made way for the SOLATECH and PETRITECH processes, which likewise came to be consigned to the past.
For the past five years, the QUASI-SEC process has been in use. This produces the ultimate waste in the form of stabilized sand.
The advantage of this process is the low rate of burial of waste in engineered landfill sites (1.2 tonnes per processing year).
The SEMI-DRY system is particularly aimed at waste that cannot be treated by other techniques.